Garages are valuable home additions that provide extra living and storage space. With strategic planning, building permits, and the right tools, you can build a garage that suits your needs.
Whether you have a classic car collection or a cherished set of power tools, building a garage is a great way to maximize storage space and protect your vehicles. Adding a garage can also boost home value—no wonder over 70% of home buyers prefer a house with one.
Building your garage can be a fun renovation project but requires careful planning and knowledge. From the permit process to construction tips, our step-by-step guide will show you how to build a garage from the ground up.
Factors to Consider Before Building a Garage
Building a garage from scratch is a big home improvement project that requires proper planning and consideration.
How you design and build your garage depends mainly on your specific priorities. Will it be used for parking, storage, or both?
Having the answers to these and other questions before building your garage from scratch will directly impact several factors that ensure your project goes smoothly.
Let’s look at the most important factors to consider:
Size
Correctly sizing your garage is one of the most critical parts of the project. A bigger garage will require more space, materials, and labor and will take longer to build. A smaller garage may end up being too small to fit your vehicle.
The best garage size depends on your vehicles and needs. Building a garage for a small sedan isn’t the same as building a garage for an SUV plus storage.
The following table shows the most common standard garage sizes by the number and type of vehicle.
Garage Size | Width | Depth | Area (square feet) |
---|---|---|---|
1-car garage1 | 12’–18’ | 20’–30’ | 240–540 |
2-car garage1 | 20’–24’ | 20’–30’ | 360–660 |
3-car garage1 | 30’–36’ | 20’–30’ | 600–1,260 |
4-car garage1 | 40’–48’ | 20’–30’ | 800–1,600 |
Trailers2 | 20’–30’ | 20’–40’ | 400–1,200 |
RVs (Classes A, B, B+, C, Super C )2 | 12’–26’ | 24’–50’ | 300–1,152 |
Sources: 1Alan’s Factory Outlet; 2Alan’s Factory Outlet
The garage’s height or roof clearance will also depend on the type of vehicle. This clearance is usually 10’–16’ high to leave enough room for the garage door and its hardware.
If you’re building a garage with extra storage space, you’ll want to choose the larger sizes, depending on your desired layout. If you plan to use your garage as a workshop or functional indoor space, it should be large enough to store equipment, tools, and furniture with sufficient walkspace.
Permits and Zoning Laws
Many communities use zoning laws to regulate how property owners use their land. You’ll almost always need a permit to build a garage and comply with setback requirements, adhering to property lines, and other local building codes and regulations.
So, before you start planning, research and check with your municipality’s Department of City Planning for the necessary information to understand the specific regulations in your area. Doing so will help you avoid costly mistakes.
When submitting a building permit application, you’ll need to include the following:
- Property survey demonstrating minimum distance requirements.
- Property specifications to show the location and proximity to the residence.
- Site plans, such as detailed drawings of the garage design and dimensions.
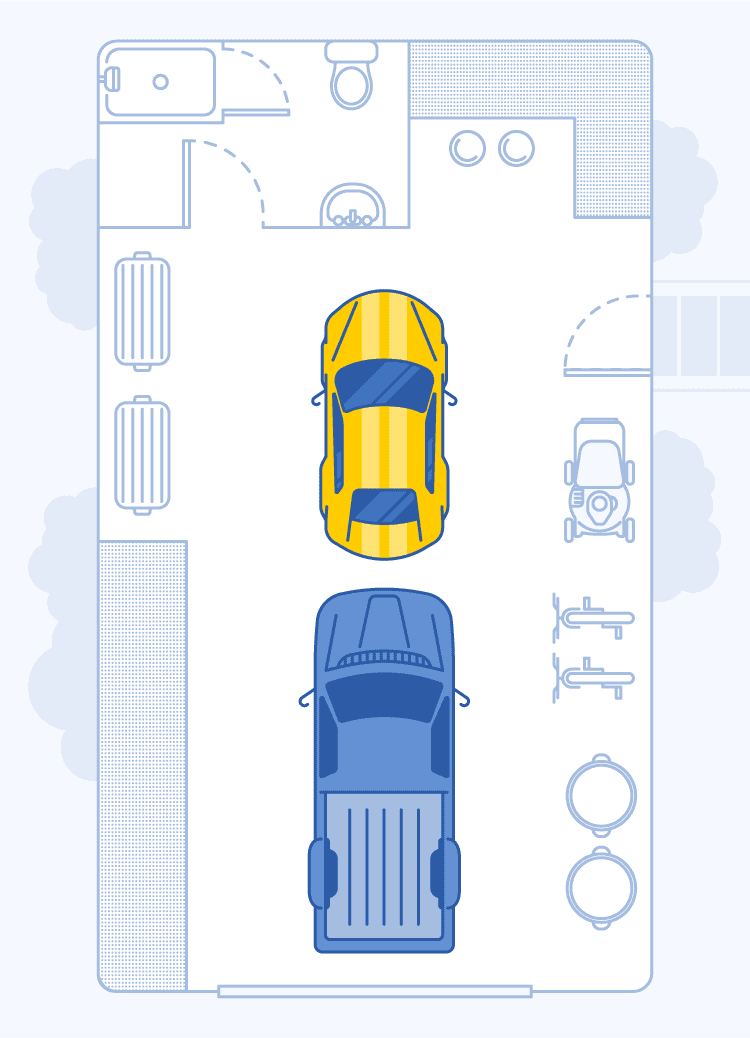
Also, be sure to check with your homeowners association (HOA). Many HOAs may have additional restrictions on the size, style, or materials you can use.
Considering the Garage Door
The garage door is a crucial element of your garage, impacting both functionality and aesthetics. Consider these factors when making your choice:
- Types and styles of garage doors: There are several types of garage doors, including roll-up, sectional (the most common), and side-hinged doors. Each has its pros and cons in terms of space, cost, and maintenance.
- Materials: Common options include wood, steel, aluminum, faux wood, composite, and fiberglass. Consider durability, insulation, and cost.
- Insulation: If you live in an area with extreme temperatures, consider an insulated garage door to help regulate the temperature inside.
- Security: Look for features like automatic locking and reinforced panels for added security.
- Automation: A garage door opener provides convenience and can be integrated with your home security system.
You must also consider the garage door size, as it’s critical to ensure it’s big enough for your vehicles. Use the following table as a reference for different sizes depending on your needs:
Garage Size | Garage Door Width | Garage Door Height |
---|---|---|
1-car garage1 | 8’–10’ | 7’–8’ |
2-car garage1 | 16’–18’ | 7’–8’ |
Trailers2 | 10’–14’ | 10’ |
RVs (Classes A, B, B+, C, Super C )1,2 | 10’–14’ | 12’–14’ |
Sources: 1A1Garage; 2Alan’s Factory Outlet
Choosing the Proper Foundation
The foundation is the base upon which your entire garage will rest. Selecting the right type of foundation is crucial for stability and longevity. When doing so, consider factors like your garage’s size and weight, the climate, soil conditions, and budget.
Here are a few common options:
- Concrete Slab: This is the most common type, offering a solid, level base. It’s suitable for most climates and soil conditions.
- Gravel: A gravel foundation is cost-effective for smaller garages or sheds. It involves compacting a layer of gravel to create a stable base.
- Pier and Beam: This foundation uses concrete piers or posts to support a frame of wooden beams and the garage structure on top, creating a crawl space underneath.
Cost
According to HomeGuide, the cost to build a garage from scratch in 2025 ranges from $35 to $60 per square foot, with people spending an average of $19,600 to $28,200 on a 2-car garage.
Expenses will depend on several factors, such as:
- Size: square footage
- Additional features like doors, windows, etc.
- Materials used
- Utility connections
Where you put the garage on your property also matters. For example, the total cost of a detached garage is much higher, as you will need to add a separate roof and establish new utility connections.
Location
Location influences many factors, such as material availability, shipment and installation costs, climate, type of terrain, and local construction laws and regulations.
For example, Alan’s Factory Outlet’s metal garages include free shipping and installation in much of the country’s East and South.
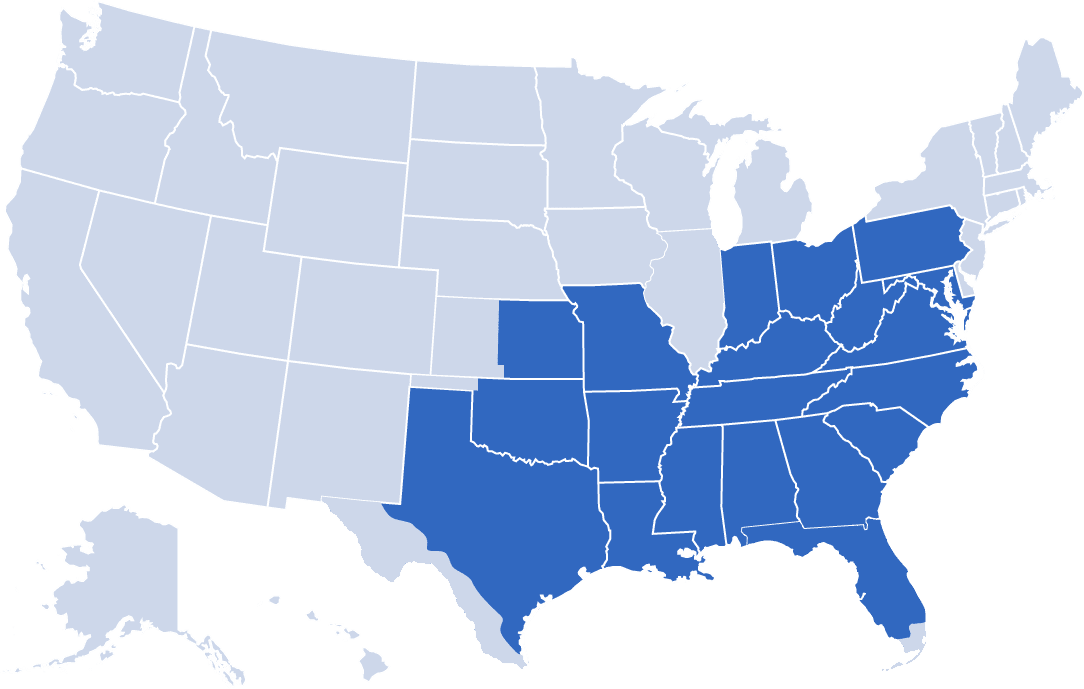
If you’re building a traditional garage and want to hire help, consider that labor costs vary significantly across the US, potentially impacting your budget.
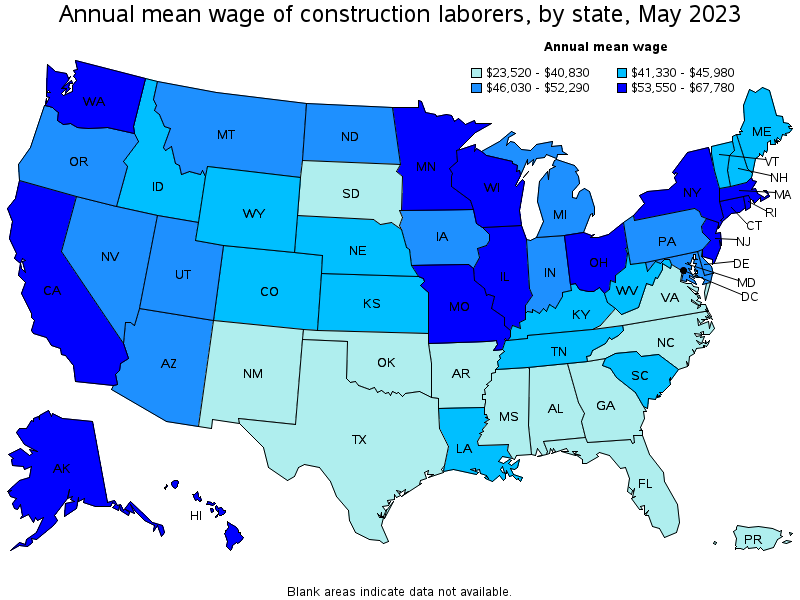
For example, according to the US Bureau of Labor Statistics, while the national mean hourly wage for construction workers is $23.69, they vary from less than $15.15 per hour to over $36.54 per hour depending on your region:
- In parts of the Southwest and Northeast, wages range from $25.75 to $32.59 per hour or $206 to $261 per worker per day.
- In the South, wages range from $11.31 to $19.63 per hour or $90 to $157 per worker per day.
- In the Midwest, you’ll pay around $19.87 to $22.11 per hour ($158 to $177 per day).
These numbers show an average 89% difference in labor costs between the Northeast and South regions.
Tools and Materials
To properly build a garage from the ground up, you’ll need to invest in different materials and tools. These depend on the phase of the building project and include the following:
Construction Phase | Tools | Materials |
---|---|---|
Foundation | Shovel, level, concrete mixer, etc. | Gravel, concrete mix, rebar, etc. |
Framing | Circular saw, power drill, hammer, etc. | Dimensional lumber, nails, connectors, etc. |
Roofing | Hammer, roofing nailer, utility knife, etc. | Roofing felt, shingles, flashing, etc. |
Siding | Circular saw, hammer, caulk gun, etc. | Siding material, nails, trim boards, etc. |
Doors & windows | Power drill, screwdrivers, etc. | Pre-hung doors, windows, garage doors, etc. |
Interior finishing | Drywall saw, screw gun, paint rollers, etc. | Insulation, drywall, paint, flooring, etc. |
Pro Tip: Unless you plan on many more DIY construction projects, renting tools can help cut costs.
How to Build a Garage in 9 Steps
Now that you have the necessary tools and permits, you can start your DIY garage project. Round up a few extra sets of hands (or hired contractors), and follow the steps in our detailed video:
Here’s a breakdown of the process in black and white:
1. Plan the Layout
The first step is to review several garage design ideas to determine which layout best suits your needs. When deciding on a design, plan for the location, prioritizing a flat and level terrain. You’ll also need to consider trees, power lines, and underground pipes on your property that may obstruct construction.
An ideal layout design should address the following factors:
- The number and size of the vehicles you’ll park inside.
- Room for storage, furniture, and walkable space/workspace.
- Length of your driveway.
- Utility connections for the intended purpose.
- Additional features like windows and garage lighting.
Consider consulting an architect or engineer to help design and draw out your garage plan.
2. Prepare the Construction Site
Site preparation is the next step before beginning the building process. It depends strongly on the type and location of the new garage and your chosen foundation.
To prepare the construction site, you’ll need to clear it of any hazardous obstructions. This includes removing debris and trees from the designated area and digging out any uneven high spots.
Pro Tip: If you need to demolish any existing structures, check with your city first to see if it requires any additional permits.
After clearing the site, stake out the desired elevation for your garage slab. Use a level and string line to create a reference plane. Carefully remove or add soil to achieve the desired grade, ensuring proper drainage away from the foundation. Once graded, compact the soil using a plate compactor or tamper to ensure a stable base for the foundation and prevent future settling.
3. Build the Foundation
The next step in building a garage is building your chosen foundation. The most common type of foundation for a garage is a poured concrete slab so it’ll be this section’s focus.
Concrete is fire- and insect-resistant and is also the most suitable and stable base for areas with poor drainage and a high risk of earthquakes.
If hiring a professional for the concrete work, you can skip to step four.
If you’re installing the slab yourself, start by sizing it correctly. Use our concrete pad size calculator to get the dimensions of the slab based on your desired garage size.
Some of the tools and supplies you’ll need for a concrete pad include:
Tools | Materials |
---|---|
Shovels and spades | Gravel |
Wheelbarrow | Concrete mix |
Measuring tape | Metal rebar |
Level | Form boards (if needed) |
String line | Vapor barrier |
Plate compactor or tamper | |
Concrete mixer (if needed) | |
Concrete pourer | |
Screed | |
Hand float and trowel |
Calculate the amount of concrete you’ll need based on the size and thickness of the slab. Our pre-mixed concrete bags slab calculator is a handy tool for this step.
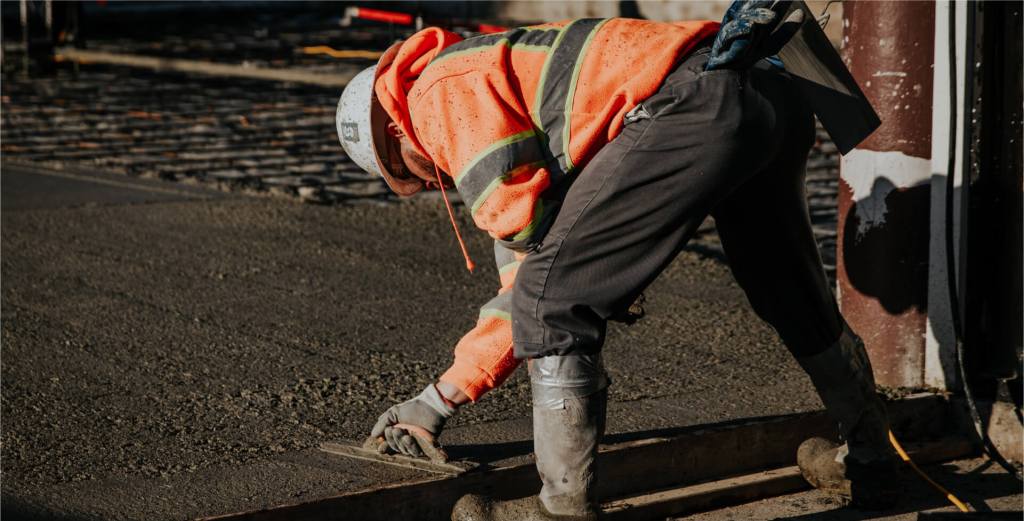
Once you have everything, follow these basic steps:
- Build forms: Create a frame to contain the concrete.
- Mix concrete: Combine cement, aggregate, and water (or use pre-mixed).
- Pour concrete: Fill the forms evenly.
- Screed: Level the surface with a screed board.
- Float: Smooth the surface with a hand float.
Keep in mind that concrete slab foundations can take up to a week to cure properly. Be sure to allow enough time for the foundation to cure before beginning the framing process.
4. Frame the Structure
After the concrete foundation is cured, framing can begin. This will serve as the garage’s structural support. Wood, steel, brick, and concrete are the most common building materials used to build a garage.
Use a saw to cut the framing materials to size, ensuring you use the correct blade for the type of material. If you’re following a garage kit diagram, assemble the framing according to the manufacturer’s instructions. Otherwise, follow these steps:
- Attach the sill plate to your foundation.
- Install floor joists, if applicable.
- Install subflooring (plywood), if applicable.
- Install vertical posts or “studs” where you’ll place the interior and exterior walls.
- Leave openings for your doors and windows, taking this opportunity to install window sills and headers.
- Raise the walls and attach the top plates.
- Attach the ceiling joists, tie beams, and rafters.
Once you have a secure frame, you’re ready for the next step.
5. Install the Roof
Once the framing is in place, move on to the roofing portion. Begin by ensuring your walls are level, followed by laying down a water-resistant membrane on the top plate of the walls. This initial layer provides a critical barrier against water infiltration.
Next, start laying your roof decking or “sheathing” material of choice, such as metal roof panels and asphalt shingles. Begin at the eaves (the lowest edge) and work your way up the roof, ensuring proper overlapping and nailing each shingle securely. Install flashing around chimneys, vents, and valleys to prevent leaks in these critical areas.
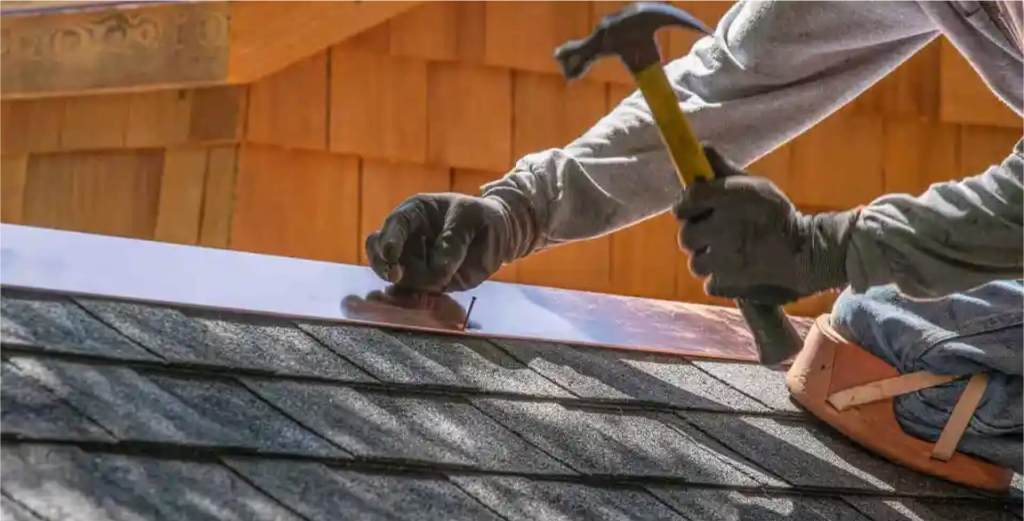
6. Install Doors and Windows
Install pre-hung windows and doors into the respective garage frame openings according to manufacturer instructions. Test them to ensure they’re properly sealed and secure.
7. Add the Siding and Exterior Finishing
Complete the exterior by installing exterior wall sheathing (e.g., plywood) followed by your siding material of choice (vinyl, wood, metal, etc.). Follow the manufacturer’s instructions for installation, ensuring the sheathing is securely fastened with no gaps.
For the siding, you’ll generally start at the bottom and work your way up, ensuring there is proper overlapping and fastening of each panel. Finally, install corner trim pieces and the window and door trim for a finished look. Don’t forget to caulk in gaps to prevent leaks.
8. Add Interior Finishing (Optional)
Once you complete your garage´s outer structure, you can install electrical wiring. Unless you have professional electrical experience, leaving this step to a certified electrician is best.
After that, you have the option to transform the “bare bones” of your garage into a functional indoor space with interior walls and floors:
- Add insulation (if desired) between the framing to help regulate the temperature inside. Common types of garage insulation include fiberglass, spray foam, and double bubble.
Safety Tip: Many insulation types are harmful if inhaled or if they come into contact with the eyes and skin. Read all instructions carefully, and wear proper personal protective equipment.
- Choose your desired wall and ceiling finishes, such as drywall and paint, for a clean and finished look.
- For the garage floor, choose a durable and low-maintenance material like epoxy coating or tiles.
9. Install the Garage Door
Following the manufacturer’s instructions, carefully assemble your garage door sections, tracks, and hardware. You may also need to attach the springs and rollers to the door frame. Carefully lift the assembled garage door into the opening and secure it to the mounting brackets on either side. Adjust the springs and opener as needed.
The last and final step is to test your garage door’s opening and closing functionality, including any automatic opener system. Keep in mind that garage doors are heavy, so consider having a helper for this step.
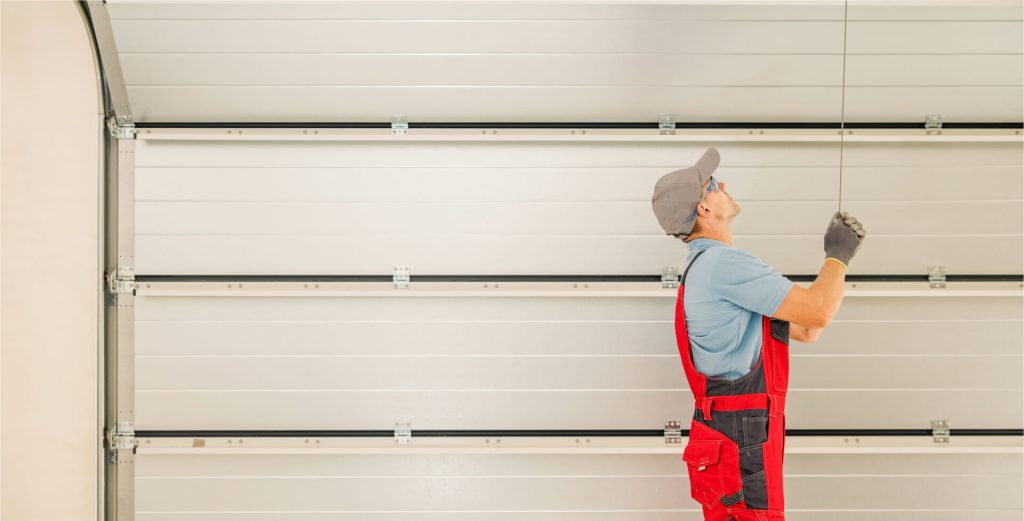
How to Build a Garage While Saving Money
Building a garage can be a significant investment, but there are ways to keep costs down without compromising quality. Here are some tips:
- Consider prefab garages: Prefab garages or garage kits are a cost-effective and time-saving alternative to traditional construction.
- Shop around for materials: Compare prices at different stores, and consider using reclaimed or recycled materials to reduce costs.
- Optimize material usage: Carefully plan and optimize material usage to minimize waste.
- Explore alternative foundation options: Explore alternative foundation options, such as a gravel foundation, which can be more affordable than a concrete slab.
- Consider your labor options: Save on labor costs by tackling some of the construction yourself, but hire a contractor for specialized tasks.
- Balance cost and quality: Evaluate the cost differences between different material options, as higher-quality materials may offer better longevity and require less maintenance.
By carefully planning your project and exploring cost-effective options, you can build a functional and durable garage without breaking the bank.
How to Maintain Your Garage
Once your garage is built, proper maintenance will ensure it lasts long and always looks its best. Here are some essential maintenance tips:
- Regular cleaning: Sweep the floor regularly to remove dirt, debris, and leaves. Wash the walls and windows periodically to prevent grime buildup.
- Inspect for damage: Regularly inspect the roof, siding, and foundation for any signs of damage, such as cracks, leaks, or rot. Address any issues promptly to prevent further deterioration.
- Garage door maintenance: Lubricate the moving parts of your garage door, including the tracks, rollers, and hinges, to ensure smooth operation. Check the springs and cables for wear and tear and have them replaced if necessary.
- Garage door opener maintenance: Test the safety features of your garage door opener regularly. Keep the opener’s remote controls clean and replace batteries as needed.
- Seasonal care: In winter, clear snow and ice from the roof and around the garage door to prevent damage. In summer, ensure proper ventilation to prevent moisture buildup.
These simple maintenance practices can keep your garage in top condition for years to come.
Building a Garage FAQ
Is it cheaper to build or buy a garage?
While you’ll spend on average $28,000 to build a garage from the ground up, buying a pre-built or “prefab garage” can cost as low as $6,500 and is a cheaper alternative.
What is the cheapest construction method for a garage?
Prefab garage kits and post-frame construction are two cheaper alternatives for building a garage. Both methods require fewer building materials and are much quicker to assemble than the traditional site-built garage.
Can you build a garage by yourself?
Building a garage by yourself is possible with the right tools, equipment, and planning. However, certain steps of garage construction require professional experience, such as site excavation, electrical wiring, and certain installations. If you want to DIY a garage project, the easiest method is with a pre-built garage kit. While you’ll spend on average $28,000 to build a garage from the ground up, buying
a pre-built or “prefab garage” can cost as low as $6,500 and is a cheaper alternative.
What is the cheapest construction method for a garage?
Prefab garage kits and post-frame construction are two cheaper alternatives for
building a garage. Both methods require fewer building materials and are much
quicker to assemble than the traditional site-built garage.
Can you build a garage by yourself?
Building a garage by yourself is possible with the right tools, equipment, and planning. However, certain steps of garage construction require professional experience, such as site excavation, electrical wiring, and certain installations. If you want to DIY a garage project, the easiest method is to use a pre-built garage kit.
Customize and Order Your Perfect Garage
If a DIY garage project is too expensive or not your thing, prefab metal garages are the next best thing. These prefabricated structures are a fraction of the cost of building a garage, saving you time and money.
From multiple sizes and colors to various features and roof styles, prefab garages are fully customizable to meet your needs. Best of all, these high-quality metal buildings are fireproof, weather-proof, and rot-resistant. can
When you order your metal garage through Alan’s Factory Outlet, we offer both free shipping and installation, giving you the best bang for your buck. Use our garage customization tool to explore the possibilities.