Jesus said that a wise man builds his house on a rock. Likewise, a wise homeowner builds his garage on a concrete slab.
If your local building department allows it, you can have a metal garage installed directly on the ground or on a gravel foundation (the installers can securely anchor the garage to the ground with rebar anchors or mobile home anchors). A dirt or gravel foundation might be fine for storing farm or garden equipment, but if you’re planning on using your garage for your vehicles, concrete is the way to go.
On my website, you might see the option to install on an asphalt foundation. That option is for carports. Because asphalt gives off a chemical smell, it isn’t suitable for an enclosed garage that isn’t well-ventilated.
Your foundation will be the second largest part of your total cost. If you’re concerned that the cost of your foundation will make your garage unaffordable, I’ve included some do-it-yourself tips at the end of this chapter.
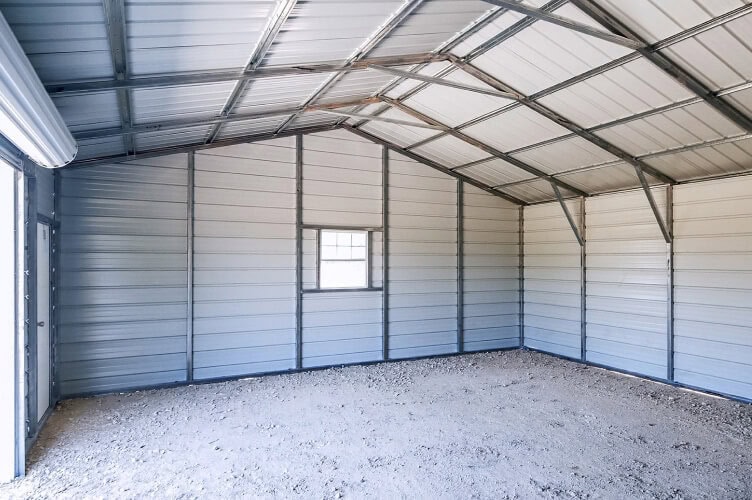
Have an Existing Foundation?
If you have an existing foundation, you might be able to use it for your new garage. Check with your local building department to verify that it meets local building codes. If you’re ordering a garage from Alan’s Factory Outlet, the foundation should usually be at least a foot wider and a foot longer than the dimensions of your garage. This will allow the garage to be securely bolted to your foundation.
Specs for Pricing a New Slab
In order to get accurate quotes for your foundation, you’ll need to know a few details about garage foundations so you can ask the right questions. Having some knowledge about foundations will also help you recognize whether the contractor you’re speaking with is an amateur or a pro.
Thickness. A four-inch-thick concrete slab is suitable for most garage foundations, but local codes may require a thicker slab. If you need to park unusually heavy vehicles in your garage (like an RV), then your foundation should be six inches thick.
If you will be using heavy-duty floor jacks to lift vehicles in your garage, you may need additional support in the areas where you will place the jacks. Discuss your specific load requirements with a concrete contractor.
Footings. The concrete around the edges of your slab will need to be thicker than the rest of the pad in order to form a footing that will support the garage walls. Typically, local codes will require a footing that is at least 12 inches deep and 12 inches wide. Deeper footings may be required in your area if you have a lower frost line or other adverse conditions.
Slope. Your foundation slab should be completely level. This ensures that the building is properly installed, doors function smoothly, and you have a flat work surface. Additionally, a level slab is the most cost-effective type to pour.
If you’re wondering why attached garages have a few inches of slope from back to front, the reason is to allow water to run out of the garage. An attached garage will often have a water heater and a washing machine that need to be drained for repair, so this is important. But for a detached metal garage, a level floor is better. If you want to wash out your garage occasionally, you can use a squeegee to sweep excess water out of the garage.
Size. Most of the metal buildings that I sell require a concrete slab that is one foot wider and one foot longer than the base of the garage. This ensures that the heavy-duty concrete bolts that anchor the garage to the ground won’t crack the concrete near the edges of the pad.
However, some of the garages I sell require a concrete pad that is the exact size of the base of the building. So I created a concrete pad size calculator that you can use to easily determine the right size of slab for a garage in your specific location.
Edges. In most locations, the engineers who design our garages recommend a concrete pad that is larger than the base (footprint) of the garage. Recommendations vary based on location and building size. You can use our concrete pad size calculator to get an initial understanding of the concrete pad required for your building.
If your concrete pad is larger than the base of your garage, it creates a 6-inch “curtain” around the edges of your garage. If this curtain is level with the rest of the foundation, water running down the outside walls of the garage will tend to pool around your garage and seep in under the bottom rail of the frame.
One method we’ve found to prevent this water leakage under the framing is to slope the 6-inch curtain downward very slightly. You can also step down the concrete by ¾ of an inch and create a ledge. Note: It is very important that if you slope the concrete curtain or create a ledge, that your level portion of the slab is large enough for the footprint of the building.
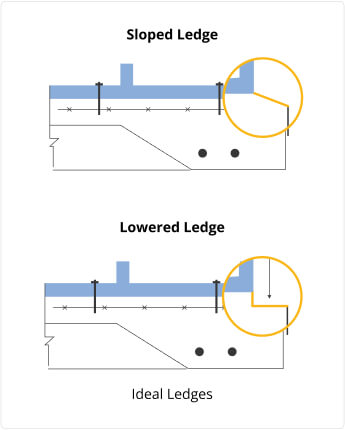
The person who builds the frame for pouring your slab can form a sloped or lowered ledge by placing six-inch boards inside the form boards, ¾” of an inch lower than where the top of the slab will be. If you decide to leave the ledges at the same level as the rest of the slab, you should apply a concrete sealant around the base rail of your garage after it is installed to prevent water from seeping into the garage.
Gravel. Compacted gravel provides a stable, level base for a concrete slab. It also helps prevent moisture in the ground from seeping into your foundation. I recommend putting down gravel before you pour a slab, but it may not be required in your area.
Vapor Barrier. Most contractors will place a thin vapor barrier on top of the gravel (or dirt), and will pour the concrete on top of this vapor barrier. The vapor barrier serves two purposes. First, it can help ensure a stronger slab by preventing water in the concrete from draining into the gravel while the concrete is curing.
The second purpose of the vapor barrier is to reduce the amount of water that can seep up from the ground, through the porous concrete slab, and into your garage. Ground moisture is especially a concern if you won’t have any gravel under your concrete slab.
Apron. You will probably need a concrete apron in front of your garage to serve as a ramp up to the top of the slab, which should be a few inches above ground level. If you also want a driveway, now is the time to figure out how large you want it to be.
Get Quotes
The easiest way to find a good concrete contractor is to call the nearest Ready Mix supplier. Talk to the concrete dispatcher and ask for the names of the best two or three concrete slab contractors in the area. The dispatchers usually know who does good work since they deliver concrete to everyone.
If you can’t get good recommendations from a concrete supplier, just do an internet search for “concrete contractor near me.” In the search results you’ll find lots of “middleman” sites like HomeAdvisor, Angi, Thumbtack, and Handy. These sites will offer to give you quotes from local professionals if you fill out a form on their website.
What you may not realize is that most of these sites will sell your contact information to several contractors. Each contractor has to pay expensive fees that can run over a hundred dollars, just to call you. If these middleman sites show you a list of local companies, you can just look up each company online to find their website or phone number instead of filling out forms to get quotes.
When you call each contractor, here’s a list of talking points to get the information you need:
- Ask if they pour foundations for detached metal garages.
- Ask them how many garage and carport foundations they do a year.
- Explain your project and ask for their recommendations.
- Ask if they recommend gravel and/or a vapor barrier.
- Ask how they cure the concrete after it is poured.
- Get a quote. Make sure you know what is and is not included in the quote.
- Ask for some recent references (homeowners who they poured a garage floor for).
Let each contractor talk enough for you to get a feel for whether they would be a good fit for your job or not. Take good notes, so you’ll know who to call back later when you’re ready to start.
Want to Do It Yourself?
The cost of labor is the biggest factor in the price of your garage foundation. If you can’t afford to hire a professional, you may be able to cut your cost in half by pouring the foundation yourself.
But remember, the foundation is a critical part of your garage, and mistakes can be expensive.
If you have plenty of time available and are willing to learn, I recommend you do two things before you decide to pour your own foundation:
Calculate the cost of materials
Use a concrete slab calculator, and a slab installation cost calculator to estimate the amount and cost of materials you will need.
Learn from a pro
It’s better to learn exactly what you need to do from a pro than to make expensive mistakes. There’s a guy named Mike Day who has an online concrete slab course for a reasonable price. It comes with a money-back guarantee, so if you take the course and decide that the job is more than you can handle, you can get a refund.
If you’ve read this far, well done. I know it’s a lot of information, but necessary to share since your garage’s foundation is so crucial. In the next chapter, I’ll share multiple options for financing your new garage.